Who we are
Laser cleaning machine website is a website specializing in providing laser cleaning equipment and services. We are committed to providing customers with advanced laser cleaning technology to help them solve various cleaning problems. Laser cleaning technology is an efficient and environmentally friendly cleaning method that removes various dirt and surface coatings. Whether you need to clean metal, non-metal, wood or other materials, we have laser cleaning equipment to meet your needs. Welcome to visit our website to learn more about laser cleaning technology, choose the product that suits you best, and make cleaning more efficient and environmentally friendly!!!
Read moreProducts on sale
Fiber-Laser-Marking-Machine
Fiber-Laser-Marking-Machine
Handheld laser marking machine | Mini portable laser marking machine
Fiber-Laser-Marking-Machine
20W all-in-one laser marking machine for sale | Special price!
Fiber-Laser-Marking-Machine
Fiber-Laser-Marking-Machine
Dynamic Focusing 3D Fiber Laser Engraving Machine for Sale at Cost Price
Fiber-Laser-Marking-Machine
Fiber-Laser-Marking-Machine
Desktop UV Laser Marking Machine for Plastic, Silicon, Glass, Ceramic
Laser marking machine
CO2 RF Laser Marking Machine with 30W America Synrad Laser Tube
NİYƏ BİZİ SEÇİRSİNİZ
80
technology patents
15
years of experience
300
R&D team
100
After-Sales Team
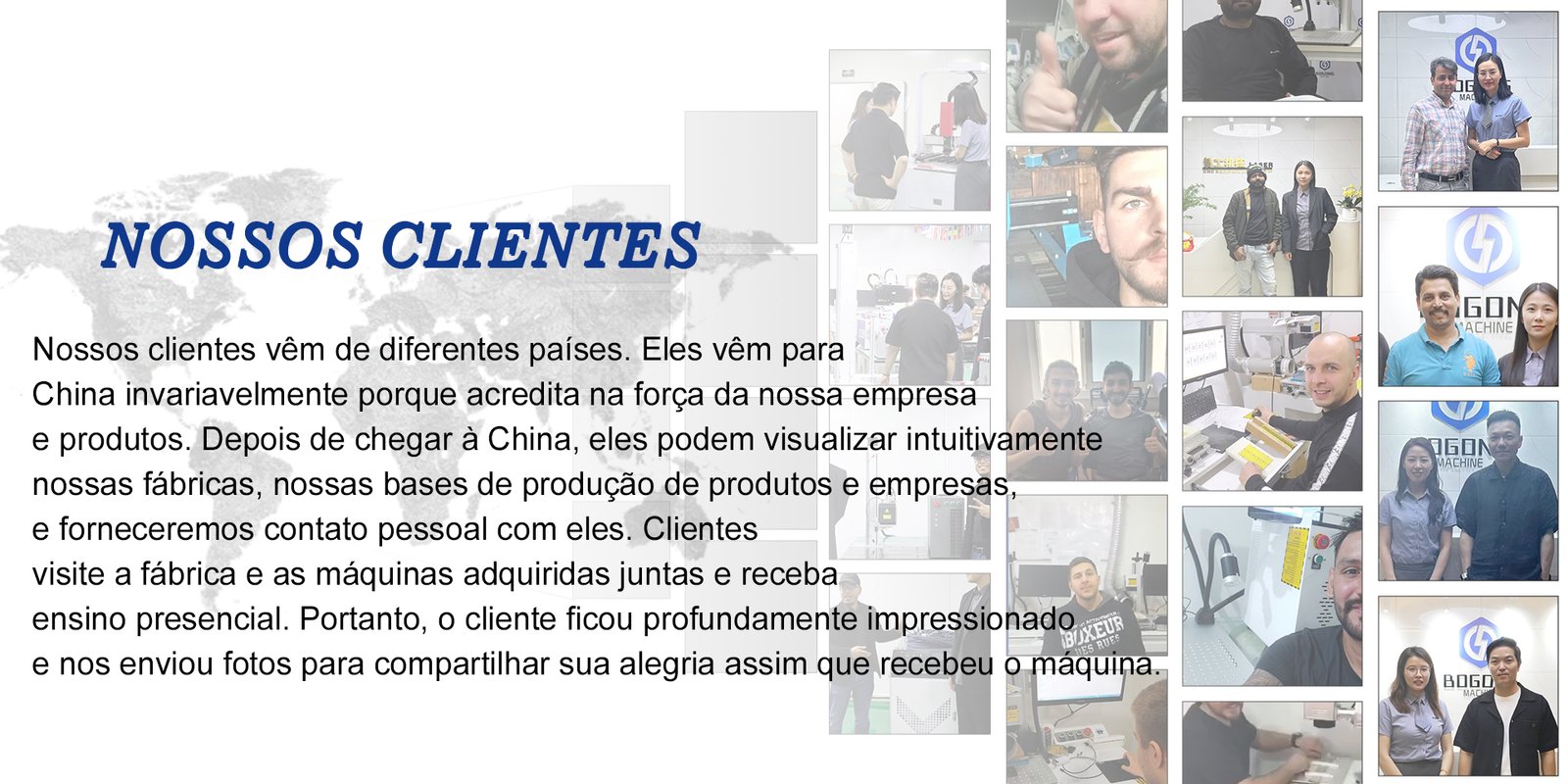